1) Large opening work: Let the regulating valve work as far as possible at the maximum opening, such as 80%. Thus, cavitation, erosion, and the like occur on the head of the spool. As the spool is broken, the flow rate increases, and the corresponding valve is closed again. This is continuously destroyed and gradually closed, so that the entire spool is fully utilized until the root of the spool and the sealing surface are broken and cannot be used. At the same time, the large opening degree of the throttle opening is large, and the erosion is weakened. This allows the valve to work at the intermediate opening degree and the small opening degree to increase the life of the valve by more than one to five times. If a chemical plant adopts this method, the service life of the valve is increased by 2 times.
2) Decrease S to increase the working opening: decrease S, that is, increase the loss of the system except the regulating valve, so that the pressure drop distributed to the valve is reduced. In order to ensure the flow through the regulating valve, the opening of the regulating valve is inevitably increased. At the same time, the pressure drop on the valve is reduced, so that cavitation and erosion are also weakened. The specific methods include: the orifice plate is throttled after the valve, and the pressure drop is consumed; the manual valve connected in series on the pipeline is closed, and the valve is obtained to obtain a better working opening. This method is very simple, convenient and effective when the valve selection is at a small opening.
3) Reduce the caliber to increase the working opening: increase the working opening by reducing the diameter of the valve. The specific methods are as follows: 1 change the valve of a small one-caliber, such as DN32 to DN25; 2 the valve body does not change , replace the valve seat with small seat diameter. If a chemical plant is overhauled, the throttle dgl0 is replaced with dg8, and the service life is doubled.
4) Transfer destruction position: Transfer the severely damaged place to the secondary position to protect the sealing surface and the throttle surface of the valve seat.
5) Growth throttling channel: The simplest way to increase the throttling channel is to thicken the valve seat, so that the valve seat hole grows to form a longer throttle channel. On the one hand, the sudden expansion after the flow-closing type of throttling can be postponed, and the position of the transfer is destroyed to make it away from the sealing surface; on the other hand, the throttling resistance is increased, the degree of recovery of the pressure is reduced, and the steam is reduced. The eclipse weakens. Some design the valve seat hole as a stepped, wave type, in order to increase the resistance and reduce the cavitation. This method is often used when introducing high pressure valves in the installation and retrofitting old valves, and is also very effective.
6) Change the flow direction: the flow-opening type flows toward the opening direction, and the cavitation and erosion mainly act on the sealing surface, so that the sealing surface of the valve core and the valve seat is quickly damaged; the flow-closing type flows toward the closed direction, and the steam After the throttling, the erosion and erosion are below the sealing surface of the valve seat, which protects the sealing surface and the root of the valve core and prolongs the life. Therefore, when the valve for the flow-open type is used, when the problem of prolonging the life is more prominent, the life can be extended by one to two times by simply changing the flow direction.
7) Use special materials: for anti-cavitation (destruction of shapes such as honeycomb dots) and scouring (streamlined small grooves), special materials resistant to cavitation and erosion can be used to manufacture the throttle. This special material is corrosion resistant and can be changed to materials that are more resistant to corrosion and have certain mechanical and physical properties. This material is divided into non-metallic materials (such as rubber, PTFE, ceramics, etc.) and metal materials (such as Monel, Hastelloy, etc.).
8) Change the valve structure: Take the method of changing the valve structure or selecting the valve with longer life to achieve the purpose of improving the life, such as multi-stage pressure-reducing valve, anti-cavitation valve and corrosion-resistant valve.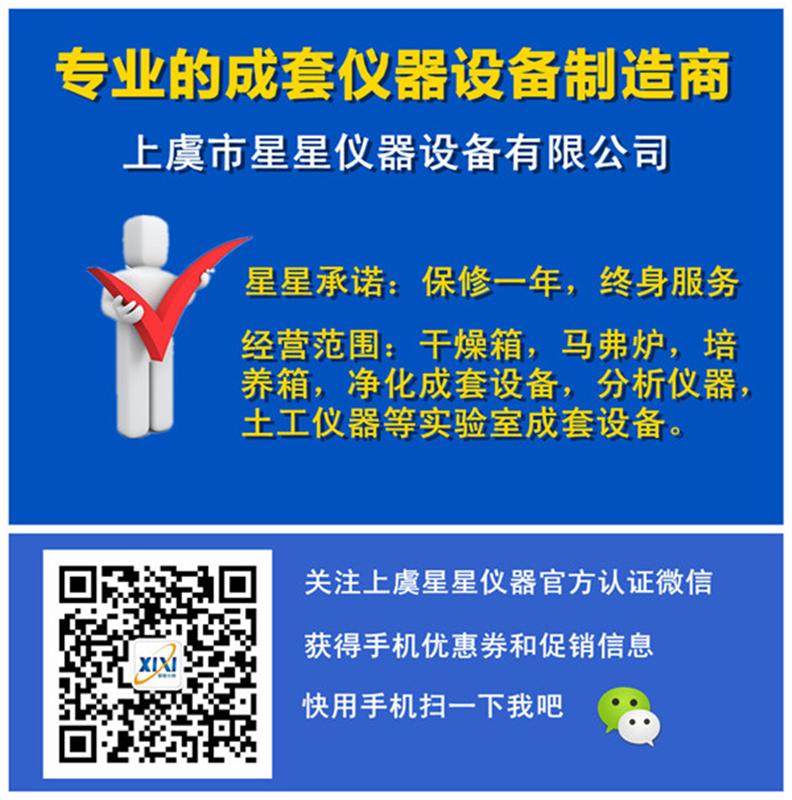
This liquid-cooled cabinet uses stable and customized insulating oil. The circulating insulating oil can absorb the heat generated by the high-power heating equipment immersed in the oil. The final heat is transferred by the high-efficiency water-cooling device. No fans are involved in the whole process (remove the cooling fan and the power supply fan) , Oil circulation uses silent high temperature resistant oil pump, efficient water circulation heat dissipation, achieves the best energy efficiency ratio of machine and liquid cooling cabinet, quiet and stable, and brings higher benefits to your business!
4 Advantages of immersion oil cooling system
1. +50% profit
2. 80% Reduced failure rate
3. Easy to install &Safe
4. Noiseless running
No fans = no noise, more profit , less downtime & less maintenance.
immersion cooling,oil immersion cooling,immersion cooling mining,immersion cooling asic,immersion cooling s19
Shenzhen YLHM Technology Co., Ltd. , https://www.sggminer.com